Exploring the Unique Properties of 1.75 ABS Filament for 3D Printers
Have you ever wondered why certain filaments stand out in the vast world of 3D printing? Well, buckle up, my dear explorer, because today, we’re diving deep into the fascinating universe of 1.75 ABS Filament.
A Stroll Down Memory Lane: History of ABS Filament
Acrylonitrile Butadiene Styrene, known fondly as ABS, isn’t just a name that rolled off someone’s tongue one fine morning. This thermoplastic polymer has a legacy that traces back decades.
Origin of ABS
The roots of ABS lie intertwined with three distinct monomers – Acrylonitrile, Butadiene, and Styrene. As scientists experimented in the early 20th century, they found that by polymerizing these three together, they could produce a plastic that combined the best properties of all three. Hence, ABS was born in the laboratories of the 1940s, initially designed for applications that needed a tough, resilient material, notably in the automotive and piping sectors.
ABS Meets 3D Printing
Now, let’s time-travel to the late 1980s and early 1990s. The realm of 3D printing was still in its infancy. The pioneers of this emerging technology were on the lookout for a reliable material to print with. They needed something that could be melted and re-solidified without losing its inherent qualities. ABS, with its melting point, durability, and fine finish, perfectly fit the bill.
This love affair between ABS and 3D printers took off dramatically. By the mid-2000s, with the rise of personal and commercial 3D printers, ABS solidified its place as one of the premier printing materials. Its ability to produce parts with a smooth finish, combined with its structural strength, made it a darling of both amateur and professional 3D enthusiasts.
The LEGO Connection
As a fun side note, think about the iconic LEGO bricks. Remember the countless hours spent building, breaking, and rebuilding? Those very bricks are made from ABS plastic. This choice isn’t accidental – ABS’s durability ensures that those bricks can be clicked together and pulled apart thousands of times without wearing out. Imagine a world where LEGO bricks break after a few uses; thankfully, the properties of ABS save the day and our childhood memories.
In essence, ABS’s rich history, from its inception in a lab to its pivotal role in 3D printing and even our cherished toys, speaks volumes about its versatility and reliability.
Why 1.75 mm, You Ask?
In the wide spectrum of filament diameters, you’d notice two main contenders: 1.75 mm and 2.85/3.00 mm. Both have their proponents, but today, let’s spotlight the darling of many – the 1.75 mm.
A Matter of Physics and Precision
The primary motivation behind any filament diameter is ensuring a smooth, consistent flow of melted plastic through the printer’s nozzle. And the thinner the filament, the less force required to push or extrude it through the nozzle. Imagine trying to sip a thick milkshake through a narrow straw versus a wider one. With the narrower straw, it takes more effort to get the shake into your mouth. Similarly, thinner filaments require less force for extrusion, which in turn can lead to more precise and consistent prints.
Wider Adoption and Choices
As the 3D printing community started leaning towards 1.75 mm filament, a self-perpetuating cycle began. More users meant more demand, which in turn led manufacturers to produce a wider variety of colors, materials, and brands in the 1.75 mm specification. This plethora of choices makes it even more appealing for newcomers to adopt.
Heating and Cooling Dynamics
Here’s a fun fact: Thinner filaments heat up and cool down faster. Why’s that important, you ask? Rapid heating ensures a quicker start to the printing process, while faster cooling translates to reduced chances of print deformities like warping or curling. A smoother printing experience? Yes, please!
Compatibility with Printer Hardware
Lastly, the 1.75 mm filament generally requires a less robust extruder mechanism due to the reduced force needed for extrusion. This makes it an ideal choice for lighter, more compact 3D printers, especially those targeted towards hobbyists or those on a budget.
In a nutshell, the 1.75 mm diameter isn’t just a random number plucked from thin air. It’s a carefully considered choice that balances physics, market dynamics, and user needs. So, next time you load that spool of 1.75 mm ABS filament, you’ll know you’re part of a legacy built on innovation and practicality. How cool is that?
The Crown Jewels: Unique Properties of 1.75 ABS Filament
When it comes to 3D printing materials, each filament type brings its unique flair to the table. However, 1.75 ABS Filament has a set of properties that, when combined, make it the star of the show.
- Durability: It’s Tough Yet Tender
- Sturdiness: Think of ABS as the athlete that endures rigorous training without batting an eyelid. It’s robust and can resist impacts, making it less prone to cracks or breaks upon accidental drops or pressure.
- Flexibility: On the flip side, ABS isn’t rigid or brittle. Its elasticity means it can bend without breaking, a trait that’s often desired in items that require a bit of give.
- Thermal Stability: Like a Rock in a Heatwave
- Resistant to Warping: One of the challenges in 3D printing is ensuring the object remains stable and retains its shape post-printing. ABS, thanks to its thermal stability, manages to reduce the infamous “warping” effect, especially when printed on a heated bed.
- Withstanding Heat: While some filaments might go soft or deform under a hot sun, ABS remains firm, making it ideal for objects exposed to higher temperatures.
- Finish & Feel: The Aesthete’s Choice
- Matte Elegance: Unlike the glossy finish of some filaments, ABS boasts a professional-looking matte appearance. This not only looks refined but also minimizes the visibility of minor print lines, lending a smoother texture to the printed item.
- Easy Post-Processing: Another crown jewel of ABS is its amenability to post-processing. You can sand, paint, or even bond multiple parts together using acetone. Imagine creating a complex multi-part model and seamlessly joining them with just a dab of acetone. Magic, isn’t it?
Chemical Resistance: Like a Duck in Water
ABS isn’t just about looking pretty or being tough; it’s also chemically resistant. This means that objects printed with ABS can resist damage from a variety of household chemicals. So, if you’re printing something that might come into contact with cleaning agents or similar substances, ABS stands tall.
In the majestic court of 3D printing materials, 1.75 ABS filament reigns supreme for many, thanks to this compelling blend of properties. Whether you’re a hobbyist or a professional, recognizing these unique attributes ensures that you harness the full potential of ABS in your creations. Ready to transform those 3D designs into tangible masterpieces?
How Does It Stack Up? Comparison with Other Filaments
In the competitive space of 3D printing materials, choosing the right filament can feel like selecting a gourmet dish from an expansive menu. Each filament brings its unique taste to the table. But how does our protagonist, 1.75 ABS filament, fare when put head-to-head with other contenders?
1.75 ABS vs. PLA (Polylactic Acid)
- Durability: While PLA is known for its rigidity, it’s also more brittle. Drop a PLA object, and you might find it shattering. ABS, with its tougher and more resilient nature, can better withstand impacts.
- Thermal Resistance: ABS wins hands down when it comes to withstanding heat. PLA tends to deform at much lower temperatures, making ABS a better choice for objects exposed to warmth or sunlight.
- Ease of Printing: PLA might have a slight edge here, as it’s often considered easier to print with, particularly for beginners. ABS, while offering superior properties, requires a more controlled printing environment, such as a heated bed, to prevent warping.
1.75 ABS vs. PETG (Polyethylene Terephthalate Glycol-modified)
- Strength and Flexibility: Both ABS and PETG are robust materials, but PETG combines strength with a slightly higher degree of flexibility. ABS, however, still offers a commendable balance of sturdiness and elasticity.
- Transparency: If you’re aiming for a semi-transparent finish, PETG is the way to go. ABS, on the other hand, is more opaque.
- Hydrophobic Properties: PETG has an edge here. Being hydrophobic, it repels water, making it suitable for moist environments. ABS, while not overly absorbent, doesn’t have the same level of water resistance as PETG.
1.75 ABS vs. TPU (Thermoplastic Polyurethane)
- Flexibility: TPU is the king of flexibility. If you’re looking to print objects that need to be bendy and stretchy, TPU is the choice. ABS, although flexible, doesn’t stretch to the extent TPU does.
- Print Speed: TPU often requires a slower print speed due to its elasticity. ABS, being less stretchy, can be printed faster without compromising on quality.
- Abrasion Resistance: TPU has excellent abrasion resistance, outdoing ABS in scenarios where the printed object might face frequent rubbing or scraping.
While 1.75 ABS filament boasts a stellar set of properties making it a versatile choice for a myriad of applications, understanding its strengths and limitations in comparison with other filaments helps in making informed decisions. So, the next time you’re gearing up for a 3D printing project, you’ll have a clearer picture of which filament will shine brightest for your specific needs. Ready to make that informed choice?
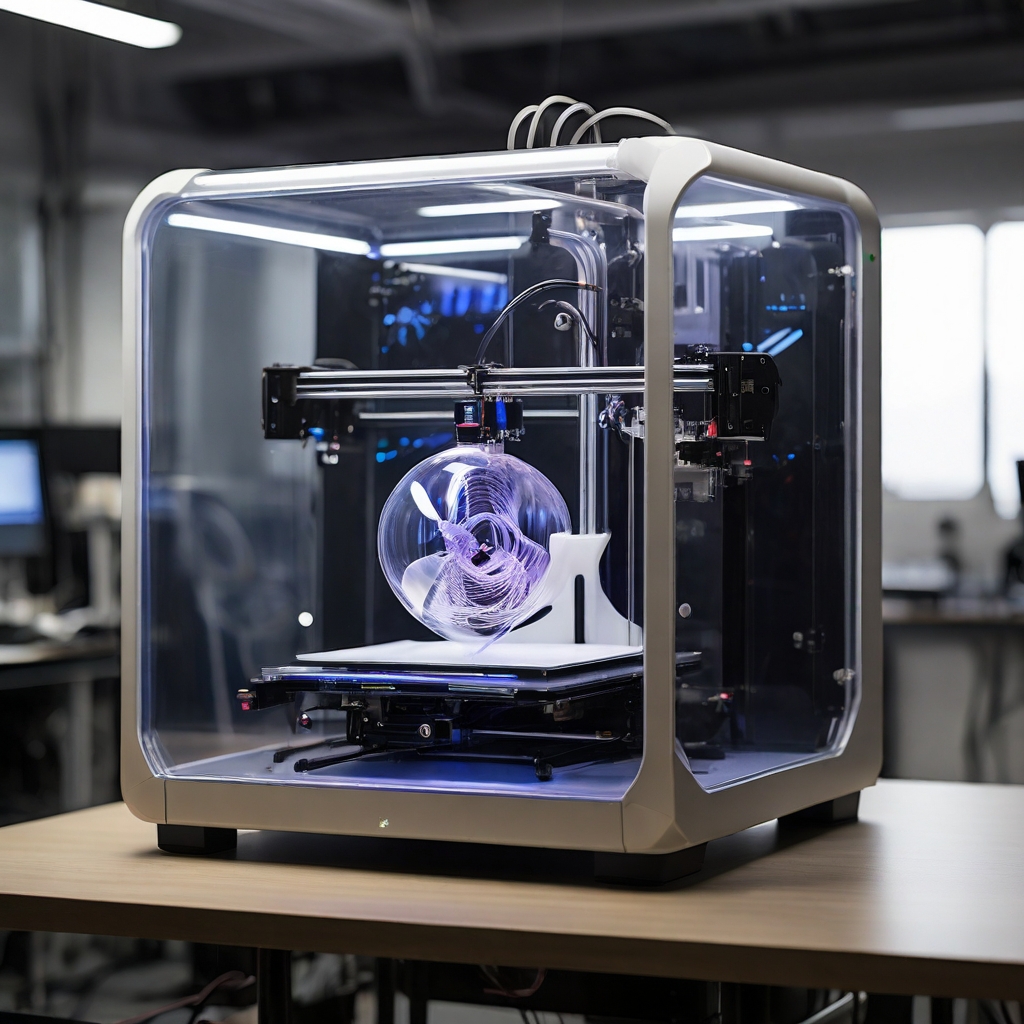
Carving Niches: Best Uses for 1.75 ABS Filament
The beauty of 1.75 ABS filament lies not just in its intrinsic properties, but also in the multitude of applications it fits into. Let’s explore where this filament truly shines.
- Prototyping: Bringing Ideas to Life
- Fine Details: ABS’s capability to capture intricate details makes it ideal for prototypes. Whether it’s a new gadget, a machine part, or a unique piece of art, ABS ensures every nuance is captured.
- Iteration-Friendly: Given the sturdy yet amendable nature of ABS, it’s possible to make iterative physical changes, like drilling, sanding, or even gluing, to fine-tune prototypes.
- Functional Parts: Not Just for Show
- Moving Parts: Think about components that need to move or fit together – gears, joints, or hinges. ABS’s strength and flexibility make it a go-to choice.
- Endurance: For parts that endure regular wear and tear, ABS’s durability comes to the rescue. Be it tool handles, protective casings, or even custom-made keychains, ABS ensures longevity.
- Automotive Components: The Need for Speed (and Durability)
- Heat Resistance: Vehicles often experience temperature fluctuations. ABS’s resistance to warping under heat ensures components retain their shape and function.
- Customization: From personalized gear knobs to custom car vents, ABS allows automotive enthusiasts to tweak and personalize with confidence.
- Consumer Products: The Everyday Marvels
- Electronics Casings: ABS’s insulative properties make it suitable for protective casings for gadgets, like custom phone cases or bespoke enclosures for DIY electronic projects.
- Toys and Collectibles: Remember the LEGO reference? ABS’s safety and resilience make it perfect for toys that are meant to be played with, not just displayed.
- Fashion and Accessories: Where Style Meets Substance
- Jewelry: ABS can be crafted into durable, unique jewelry pieces. From earrings to brooches, the material holds up well against the rigors of daily wear.
- Footwear: Think customized shoe soles or heel supports. ABS’s strength and flexibility offer comfort and longevity.
While this list paints a broad picture, the versatility of 1.75 ABS filament means the possibilities are vast and limited only by imagination. It’s this adaptability that cements ABS’s position in the pantheon of 3D printing materials. Whether you’re a professional engineer, a budding artist, or a hobbyist, there’s a good chance ABS has a special role to play in your creations. Ready to see where ABS can take your next project?
Words of Wisdom: Tips for Using 1.75 ABS Filament
Harnessing the full potential of 1.75 ABS filament involves more than just loading it into your printer. Here are some golden nuggets to help you achieve those picture-perfect 3D prints:
- Temperature Matters: Dialing it Just Righ
- Optimal Printing Temperature: While ABS generally prints between 220°C to 250°C, it’s crucial to start at the lower end and adjust based on the filament brand and your printer’s specifics. Not too hot, not too cold, just right!
- Bed Temperature: To prevent the dreaded warping, a heated bed is essential. Aiming for around 100°C ensures the first layer adheres well, setting the stage for a successful print.
- Warping Woes: Keeping Things Flat
- Use Adhesion Helpers: Consider using adhesion aids like ABS juice (a mix of ABS scraps and acetone) or specialized print bed adhesives. These ensure that your print sticks to the bed throughout the printing process.
- Enclosed Print Area: An enclosed printing environment helps maintain consistent temperatures, reducing the risk of warping. If your printer doesn’t come with an enclosure, consider DIY solutions or aftermarket add-ons.
- Ventilate, Ventilate, Ventilate!
- Good Airflow: While ABS offers fantastic properties, it can emit fumes during printing. It’s essential to ensure your printing space is well-ventilated. An open window or an exhaust fan can make a world of difference.
- Air Filters: If you’re printing in spaces without optimal ventilation, consider using printers with built-in air filters or investing in standalone air filtration systems.
- Speed and Layer Height: Balancing Quality and Time
- Print Speed: While ABS allows for reasonably fast printing, if you’re chasing finer details, consider slowing down the print speed. This ensures better layer adhesion and a smoother finish.
- Layer Height: A smaller layer height captures intricate details but can increase print times. Depending on your project’s needs, adjust the layer height to strike the right balance between detail and duration.
- Post-Processing: Giving Your Print the Royal Treatment
- Sanding: ABS sands beautifully. Start with a rougher grit and work your way to finer grits for a smooth, polished finish.
- Acetone Vapor Smoothing: For an even smoother surface, consider acetone vapor smoothing. This process involves exposing the ABS print to acetone vapors, which slightly melt the outer layer, giving it a glossy appearance.
Armed with these words of wisdom, you’re not just printing; you’re crafting masterpieces. Remember, as with any craft, patience and practice are key. Over time, you’ll develop an intuition for what works best for your unique setup and projects. Ready to elevate your 3D printing game with 1.75 ABS filament?
Conclusion: Tying the Knot
So, my fellow explorer, next time you’re gearing up for a 3D printing adventure, remember the valiant knight that is the 1.75 ABS Filament. Strong, flexible, and always ready to impress. Why choose anything less than the best?
FAQs
- Why choose 1.75 ABS over other filaments?
The combination of strength, flexibility, and thermal stability makes it a top contender in the 3D printing arena. - Is 1.75 ABS safe to use indoors?
While ABS can emit fumes, ensuring proper ventilation makes the printing process safe. - How do I store my 1.75 ABS filament?
Keep it in a cool, dry place, away from direct sunlight. A desiccant can be a good companion. - Does color matter in 1.75 ABS filament?
While color can be aesthetic, the properties of ABS remain consistent across the spectrum. - Can I mix 1.75 ABS with other filaments?
While possible, ensure compatibility and optimal printing conditions for the best results.